Classification of Oil Sludge Pyrolysis Plant
- By zhou qi
- •
- 01 Feb, 2024
Unveiling the Technological Tapestry
Batch Pyrolysis Plants: The Pioneers
The batch pyrolysis plant, while time-consuming, offers advantages in terms of simplicity and ease of maintenance. It is an ideal choice for smaller-scale operations or facilities with fluctuating oil sludge quantities. The intermittent nature of batch processing allows for meticulous control over temperature and processing conditions, ensuring optimal yields.
Continuous Pyrolysis Plants: Uninterrupted Efficiency
The continuous pyrolysis process involves a constant feed of oil sludge into the reactor, where it undergoes pyrolysis without the need for intermittent loading and unloading. This continuous operation streamlines the overall production, reducing downtime and increasing the overall yield. The automation of these plants, coupled with advanced control systems, ensures precision in processing conditions.
Feedstock Flexibility: Adapting to Variability
Conventional Oil Sludge Pyrolysis Plants
While effective for dedicated applications, conventional pyrolysis plants may face challenges when dealing with varying sludge compositions. Adapting to feedstock variability requires constant monitoring and adjustment, highlighting the need for a meticulous understanding of the sludge input.
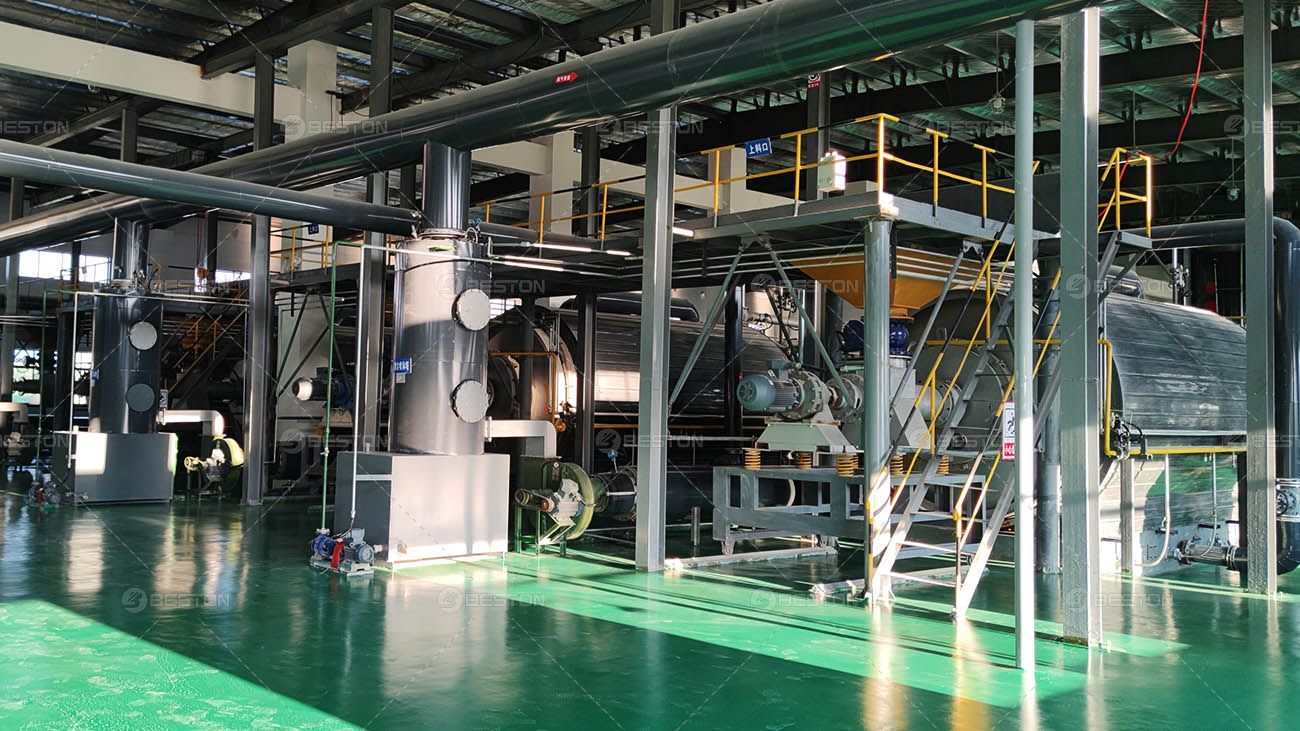
Advanced Hybrid Pyrolysis Plants
The hybrid approach combines the precision of conventional pyrolysis with the adaptability required to handle diverse sludge compositions. This adaptability is particularly crucial in industries where the feedstock characteristics may vary over time or across different sources.
Environmental Stewardship: Emission Control Systems
Catalytic Pyrolysis Plants
The catalytic process not only improves the efficiency of hydrocarbon conversion but also plays a pivotal role in reducing undesirable by-products. This contributes to a cleaner and more environmentally friendly operation, aligning with stringent emission standards and regulatory requirements.
Scaling Heights: Modular Pyrolysis Plants
Small-Scale Modular Pyrolysis Plants
The modular design allows for easy scalability, enabling businesses to expand their waste management capabilities in tandem with growing needs. The mobility of these units adds an extra layer of flexibility, allowing for on-site deployment in areas with limited infrastructure.
Large-Scale Centralized Pyrolysis Plants
Centralized plants benefit from economies of scale, optimizing the overall cost-effectiveness of waste processing. The integration of advanced technologies and extensive automation ensures seamless operations even at large scales, underlining their importance in managing significant volumes of oil sludge.
Conclusion: A Tapestry of Technological Excellence
As environmental consciousness takes center stage, catalytic and microwave-assisted technologies usher in a new era of cleaner and more efficient oil sludge pyrolysis plants. The future promises not only enhanced waste-to-resource conversion but also a continued commitment to pushing the boundaries of innovation in the pursuit of sustainable industrial practices.