Exploring the Diverse Landscape of Oil Sludge Pyrolysis Plants
- By zhou qi
- •
- 27 Feb, 2024
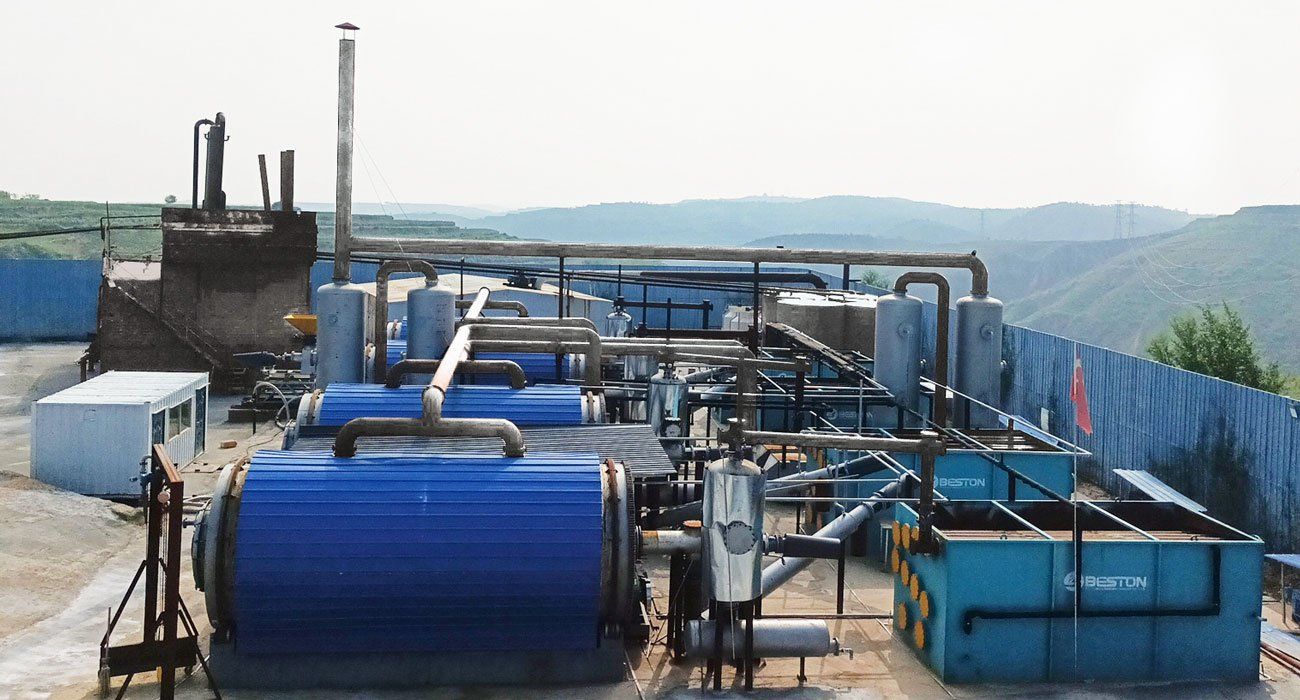
https://bestonasia.com/small-pyrolysis-machine/
https://bestonasia.com/pyrolysis-plant/continuous/
https://bestonasia.com/thermal-desorption-unit/
https://bestonasia.com/continuous-tyre-pyrolysis-plant/
https://bestonasia.com/tyre-pyrolysis-process/
https://bestonasia.com/tyre-pyrolysis-plant-manufacturers/
https://bestonasia.com/pyrolysis-plant-for-sale/
https://bestonasia.com/paper-tray-making-machine/
https://bestonasia.com/industrial-packaging-solution/
https://bestonasia.com/rice-husk-charcoal-making-machine/
https://bestonasia.com/jute-stick-charcoal-making-machine/
https://bestonasia.com/sawdust-charcoal-making-machine/
https://bestonasia.com/carbonization-machine/