How Pulp Molding Machine Works
- By zhou qi
- •
- 12 Mar, 2024
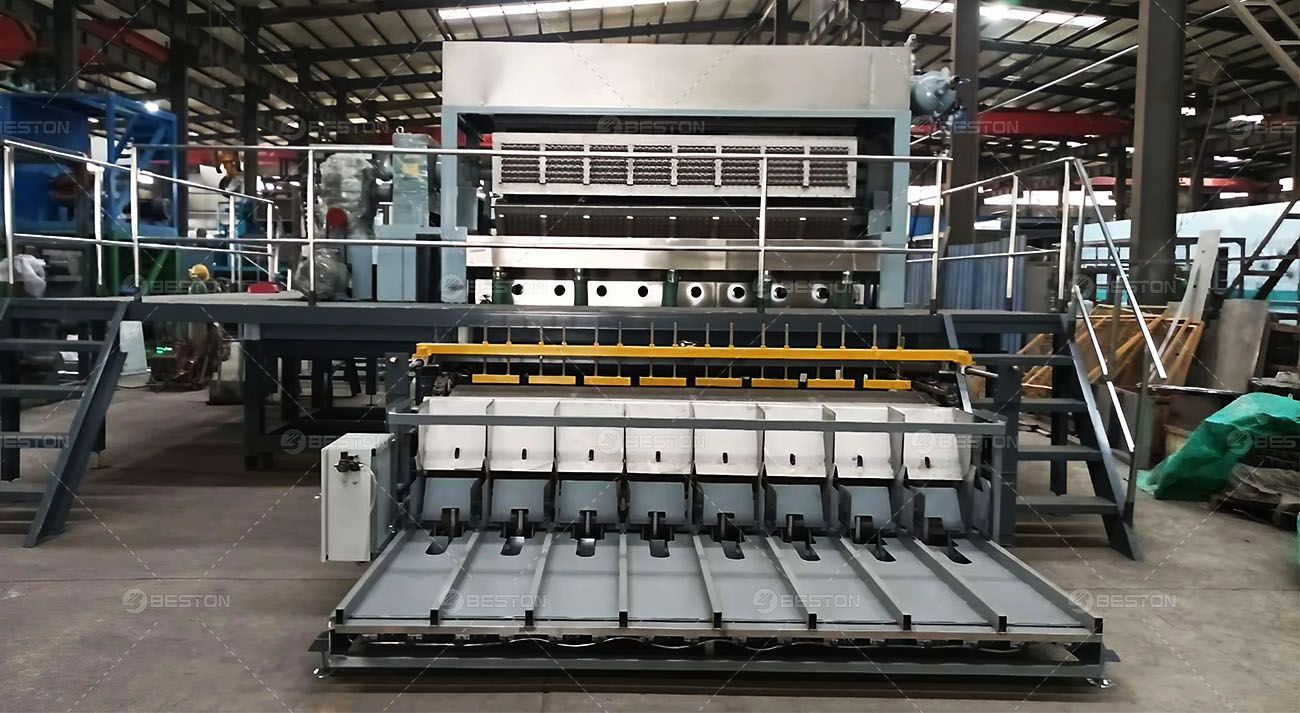
Overview of Pulp Molding Process
The pulp molding process begins with the preparation of a slurry comprising recycled paper pulp and water. This slurry is then transferred to the pulp molding machine, where it undergoes a series of steps to form, shape, and dry the desired products. The process is highly customizable, allowing manufacturers to produce a variety of designs and sizes to meet specific requirements.Key Components of a Pulp Molding Machine
- Forming Mold: The forming mold is a crucial component of the pulp molding machine responsible for shaping the pulp slurry into the desired product. It consists of a mold cavity or series of cavities that define the shape and dimensions of the final product.
- Vacuum System: The vacuum system is utilized to extract excess water from the pulp slurry during the molding process. This ensures uniform distribution of pulp and facilitates the formation of intricate details and fine features in the final product.
- Drying System: Once the products are formed, they undergo a drying process to remove moisture and solidify the pulp material. The drying system typically involves hot air circulation or infrared heating to accelerate the drying process and achieve the desired moisture content.
- Transfer System: The transfer system is responsible for moving the formed products from the molding stage to the drying stage within the pulp molding machine. It ensures smooth and efficient transition between different stages of the process.
Operation of a Pulp Molding Machine
1. Preparation of Pulp Slurry
The pulp molding process begins with the preparation of a slurry mixture consisting of recycled paper pulp and water. The pulp is obtained from various sources, including recycled newspapers, cardboard, and agricultural waste. The pulp is then blended with water to form a homogeneous mixture with the desired consistency.2. Molding Stage
Once the pulp slurry is prepared, it is transferred to the pulp molding machine for molding. The forming mold, equipped with the desired cavity configuration, receives the pulp slurry, which is evenly distributed across the mold surface. A vacuum system is activated to extract excess water from the slurry, causing the pulp fibers to adhere and conform to the shape of the mold cavity.3. Drying Stage
After the products are molded, they are transferred to the drying stage within the pulp molding machine. Here, the products undergo a drying process to remove moisture and solidify the pulp material. The drying system employs heat and airflow to accelerate the evaporation of water from the products, ensuring uniform drying and consistent product quality.4. Demolding and Finishing
Once the products are fully dried, they are demolded from the forming mold and undergo any necessary finishing processes, such as trimming or stacking. This depends on the intended use of the pulp product. For example, with an egg tray machine, this step is relatively simple.The finished products are then ready for packaging and distribution to customers.Advantages of Pulp Molding Machine
The pulp molding machine offers several advantages over traditional manufacturing processes, making it an attractive option for sustainable packaging and product manufacturing:- Environmental Sustainability: The use of recycled paper pulp as a raw material reduces the consumption of virgin resources and mitigates environmental impact by diverting waste from landfills.
- Versatility: Pulp molding machines are highly versatile and can produce a wide range of products with intricate designs and shapes to meet diverse customer needs.
- Cost-effectiveness: The use of recycled paper pulp and efficient manufacturing processes result in cost savings compared to traditional manufacturing methods, making pulp molding a cost-effective solution for packaging and product manufacturing.
- Customization: Manufacturers have the flexibility to customize product designs, sizes, and configurations to meet specific customer requirements, allowing for greater market adaptability and competitiveness.